Wood Bending and Forming Machine in 2025 Revolutionising the Woodworking Industry
The process involves several key steps of Wood Bending and Forming Machine
- Preparation of Wood Sheets/Veneers: Thin sheets or veneers of wood are selected based on the desired thickness and quality. These sheets are then moistened or conditioned to facilitate better bending during the press process.
- Heating: The wood is placed in the hot press machine, where it is exposed to heat. The heat causes the wood fibers to become more flexible, making the material easier to bend without breaking.
- Pressing: After the wood reaches the desired temperature, pressure is applied to it. This pressure is exerted uniformly, ensuring that the wood takes on the shape of the mold or the desired contour.
- Cooling: Once the wood has been shaped and the pressing process is complete, the wood is allowed to cool while still in the press, solidifying its new form.
- Finishing: After the cooling process, the shaped wood is removed from the press and any additional finishing work, such as trimming, sanding, or coating, is done to enhance its appearance and durability.
Applications of Wood Bending and Forming Machine
Hot press machines are used in a wide range of applications in the woodworking industry, particularly in the creation of custom shapes and sizes. Some of the key applications include:
- Furniture Manufacturing: Hot presses are commonly used in the production of bentwood furniture, such as chairs, tables, and cabinets. These machines help in creating smooth, ergonomic designs and ensure high-quality craftsmanship.
- Wooden Panels & Doors: Hot press machines are essential in the production of curved wooden panels and doors, enabling manufacturers to produce unique, aesthetically pleasing designs.
- Architectural Woodworking: The ability to bend and form wood allows architects to push the boundaries of design, creating complex wooden structures and facades for both commercial and residential buildings.
- Musical Instruments: Hot pressing is also used in the production of musical instruments like guitars and violins, where precise bending of wood is crucial for sound quality and structural integrity.
- Boat Building: In boat building, hot press machines allow for the bending of wooden planks to create the hulls of boats, ensuring both strength and flexibility in the construction.
Benefits of Using Wood Bending and Forming Machine
- Precision & Consistency: Hot press machines offer exceptional precision in bending and forming wood. The uniform application of heat and pressure ensures that every piece produced is consistent and meets the required specifications.
- Complex Shapes: One of the biggest advantages of hot press machines is their ability to create complex, intricate shapes. From curved furniture parts to unique architectural features, these machines allow woodworkers to push the boundaries of design.
- Improved Durability: The heat and pressure applied during the process can enhance the structural integrity of the wood, making it more resistant to warping, cracking, or breaking.
- Time Efficiency: The hot press process is relatively fast compared to traditional methods of bending wood, leading to faster production times and improved manufacturing efficiency.
- Cost-Effectiveness: While the initial investment in a hot press machine can be significant, the long-term benefits—including faster production, higher-quality output, and reduced material wastage—make it a cost-effective choice for many manufacturers.
- Eco-Friendly Process: Since the process uses heat and pressure rather than chemicals or adhesives, it’s an environmentally friendly method of bending and shaping wood.
Challenges and Considerations of Wood Bending and Forming Machine
While hot press machines offer numerous benefits, there are some challenges and considerations to keep in mind:
- Wood Type: Not all wood types are suitable for hot pressing. Hardwoods, softwoods, and engineered woods behave differently under heat and pressure, and some may require special treatment or preparation.
- Initial Investment: Hot press machines can be expensive, particularly for high-end models with advanced control systems. However, the long-term benefits often outweigh the initial costs.
- Maintenance: Like all heavy machinery, hot press machines require regular maintenance to ensure they operate efficiently. Proper maintenance ensures the machine continues to deliver high-quality results over time.
- Skill and Training: Operators need specialized training to run hot press machines effectively. A lack of proper training can lead to errors in the bending process, resulting in waste or defects.
Conclusion: The Future of Wood Bending and Forming Machine
Hot press machines are revolutionizing the woodworking industry, offering manufacturers the ability to create intricate and precise wood designs that were once thought impossible. As technology continues to improve, we can expect even greater advances in automation, precision, and efficiency in hot pressing, further expanding the possibilities of what can be achieved with wood.
For businesses and craftsmen looking to stay ahead of the curve, investing in a hot press machine for wood bending and forming is not just a choice—it’s a necessity to remain competitive in the rapidly evolving woodworking industry.
Wood Bending and Forming Machine in 2025 working video
Other video of Wood Bending and Forming Machine
video of Wood Bending and Forming Machine in 2025 | https://youtu.be/w0LU4IijRn4?si=bB4RbDTVa7myPnRc |
When purchasing a new wood bending and forming machine, it’s important to evaluate several key factors to ensure you get the best value, performance, and suitability for your production needs. Here are the key points to consider:
🔧 1. Type of Bending/Forming Method
Steam Bending: Uses heat and moisture; traditional and good for curves.
Cold Bending: Requires mechanical force; less common for wood.
Laminated Bending: Involves gluing thin layers and clamping in forms.
CNC/Forming Presses: For complex, repeatable, and precision curves.
👉 Choose based on the final product design and production method.
⚙ 2. Machine Capacity & Size
Workpiece Dimensions: Max length, thickness, and width the machine can handle.
Bending Radius Capabilities: Minimum radius achievable.
Cycle Time: Speed of forming process – affects production efficiency.
Forming Bed or Mold Size: Must suit your most common product dimensions.
🧠 3. Automation & Control
CNC or Manual Operation: CNC allows repeatability, programmable settings.
Sensors & Feedback: Helps in process consistency and error reduction.
🪵 4. Material Compatibility
Ensure the machine supports the wood types (e.g., oak, birch, beech, MDF) you plan to use.
📈 5. Production Volume and Scalability
High-volume vs. low-volume production needs.
Ability to scale operations with modular upgrades or add-ons.
🛠 6. Tooling & Mold Requirements
Interchangeable molds or jigs for different shapes.
🧰 7. Maintenance & Support
Availability of spare parts and service technicians.
Warranty terms and after-sales service.


Beam saw machines:- https://jobspaye.com/category/wood-working-machines/beam-saw/
10 panel saw for carpentry :-https://jobspaye.com/category/wood-working-machines/panel-saw/
What is the seasoning of timber:-https://jobspaye.com/what-is-the-seasoning-of-timber/
Artical Written By
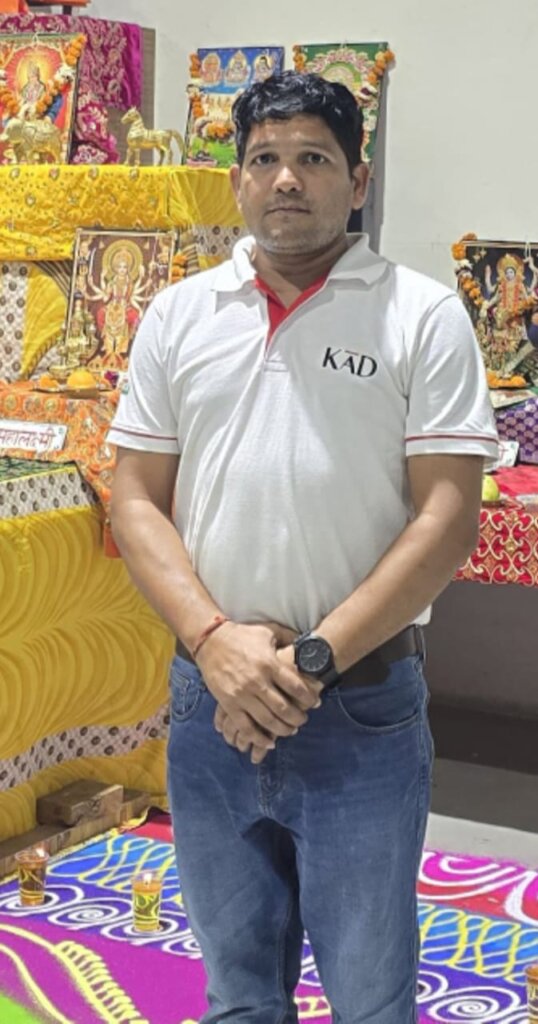