Edge Banding Machine Applications Moreover, Edge bending machines come equipped with advanced features such as automatic feeding, trimming, and buffing.
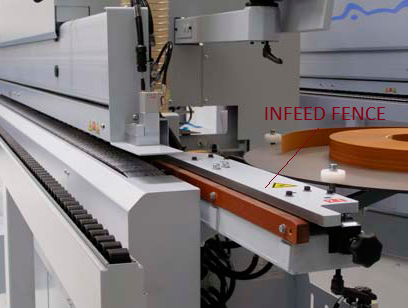
Best Edge Banding Machines application
How to Choose an Edge Banding Machine
Choosing the right edge banding machine depends on several factors including your budget, production volume, material type, and desired features
Tips for Efficient Edge Banding
Choose the Right Edge Banding Machine.
Optimize Machine Settings: Adjust machine settings such as feed speed, temperature, pressure, and trimming depth according to the type and thickness of the edge banding material you’re using. Fine-tuning these settings can improve bonding and minimize waste.
Maintain Sharp Tools: Regularly sharpen cutting blades, trimmers, and milling cutters to ensure clean and precise cuts. Dull tools can result in rough edges, increased waste, and decreased efficiency.
Train Personnel: Provide comprehensive training to operators on proper machine operation, maintenance, and troubleshooting techniques. Well-trained personnel can significantly improve efficiency and reduce downtime associated with machine malfunctions or operator errors.
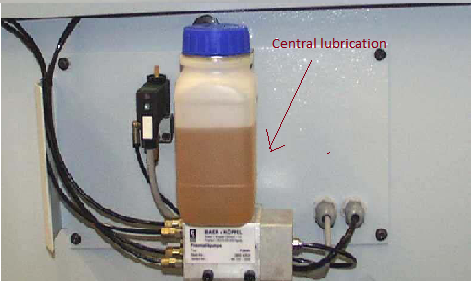
Edge banding machines, lubrication oil and grease are used to ensure smooth operation and reduce friction between moving parts. Here are some common lubricants used in edge banding machines:
Machine Oil: Machine oil, also known as lubricating oil, is commonly used to lubricate moving parts such as gears, bearings, and sliding mechanisms in the edge banding machine. It helps reduce friction, prevent wear and tear, and prolong the lifespan of machine components. Machine oil should be applied regularly according to the manufacturer’s recommendations.
Grease: Grease is a semi-solid lubricant that is used to lubricate components that require long-lasting lubrication or protection against contaminants. Grease is typically applied to components such as shafts, screws, and gears in the edge banding machine. It provides better adhesion and stays in place longer than liquid lubricants. Different types of grease are available for various applications, so it’s important to use the appropriate grease recommended by the machine manufacturer.
Chain Oil: If the edge banding machine uses chains for conveying or driving components, chain oil may be used to lubricate the chains and sprockets. Chain oil helps reduce friction, prevent rust and corrosion, and extend the life of the chains and sprockets. It’s important to regularly lubricate chains to ensure smooth operation and minimize wear.
Pneumatic Oil: Edge banding machines equipped with pneumatic components may require pneumatic oil for lubricating air cylinders, valves, and other pneumatic devices. Pneumatic oil helps maintain the performance and longevity of pneumatic components by reducing friction and preventing corrosion.
When using lubricants in edge banding machines, it’s essential to follow the manufacturer’s recommendations regarding the type of lubricant to use, the frequency of lubrication, and the proper application method. Over-lubrication or using the wrong type of lubricant can cause problems such as contamination, reduced performance, or damage to machine components. Regular maintenance and lubrication are essential for ensuring the smooth and efficient operation of edge banding machines.
Feeding Unit : This unit is responsible for feeding the workpieces into the machine at a consistent speed and alignment. It often includes conveyor belts or rollers to facilitate smooth material handling.
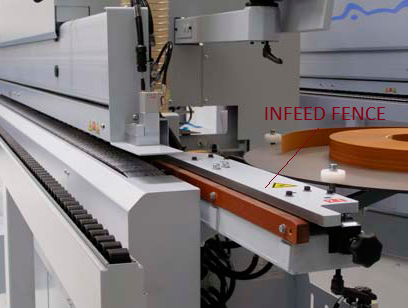
Pre-Milling Unit : Some edge banding machines feature a pre-milling unit that trims the edges of the workpieces before applying the edge banding material. This unit helps ensure clean and precise edges for optimal bonding.

Glue Application Unit : The glue application unit applies adhesive to the edges of the workpieces or to the edge banding material itself. It can use various methods such as hot melt glue, PUR (polyurethane) adhesive, or EVA (ethylene-vinyl acetate) glue.
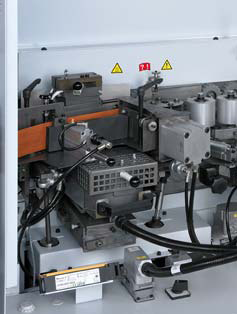
Pressure Roller Unit : The edge bending pressure roller unit plays a crucial role in this process. It typically consists of one or more rollers that apply pressure to the edge banding material as it is fed through the machine. This pressure helps to ensure that the edge banding adheres tightly to the edge of the workpiece, creating a clean and seamless finish.
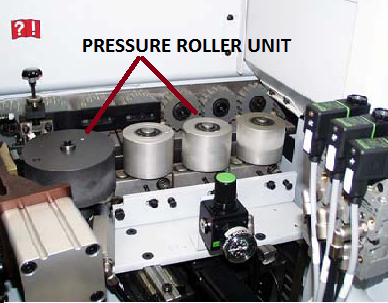
Trimming Unit : Trimming units trim the excess edge banding material from the top and bottom edges of the workpieces to achieve a clean and flush finish. Trimming can be done using various methods such as saw blades, trimmers, or milling cutters.

Corner Rounding Unit : Some advanced edge banding machines feature a corner rounding unit that rounds off the sharp corners of the workpieces after edge banding. This unit helps achieve a smooth and aesthetically pleasing edge profile.
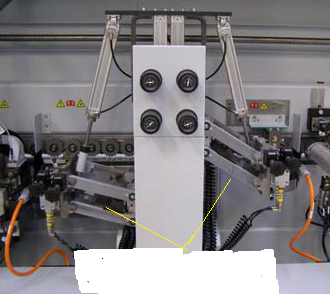
Scraping Unit : Scraping units remove any excess adhesive or material residue from the edges of the workpieces after trimming. This helps ensure a smooth and uniform edge finish.
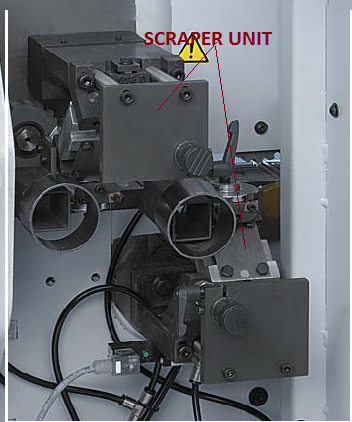
Buffing Unit : The buffing unit polishes the edges of the workpieces to remove any remaining imperfections and achieve a glossy or matte finish. It typically uses rotating abrasive pads or brushes to buff the edges.
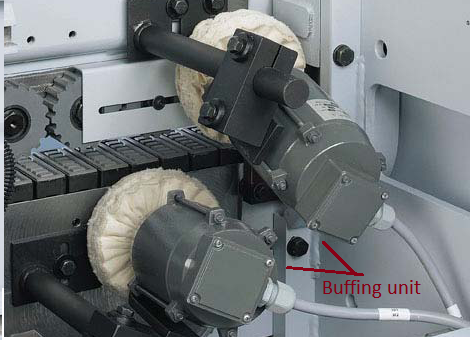
1-HOMAG edge bending https://youtu.be/aeMBFrRlGxw?si=1WitfFzmmX9Khej2
2-BIESSE edge bending https://youtu.be/0zs_k7ST-j4?si=uH78Wo9vBr6HbLv1
IMAGES and Video taken from there company website