8 types of cnc machines Breakdown:-CNC machines are complex systems, and breakdowns can occur due to various reasons, often involving one or more key components. Below is a breakdown of the main types of CNC machine breakdowns.
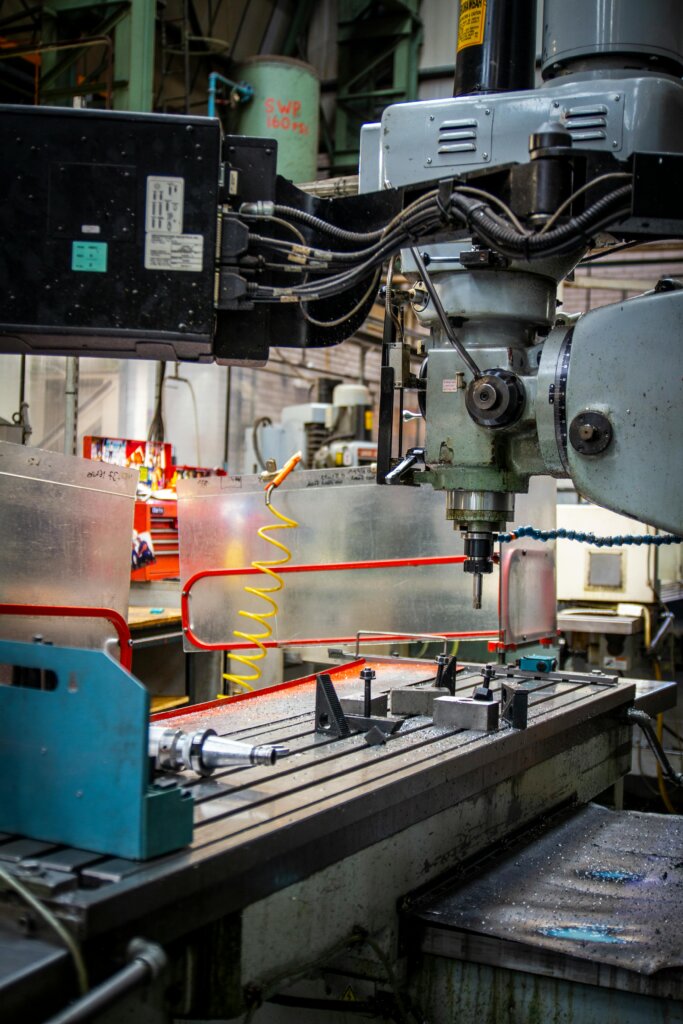
1 – Mechanical Failures cnc machines Breakdown
- Mechanical failures are often caused by wear and tear, lack of maintenance, or incorrect handling. Some common issues include.
Mechanical failures are often caused by wear and tear, lack of maintenance, or incorrect handling. Some common issues include:
Spindle Issues
Symptoms: Vibration, overheating, or strange noises.
Causes: Lack of lubrication, worn bearings, or incorrect speeds.
Solution: Inspect and replace bearings or the entire spindle assembly as needed.
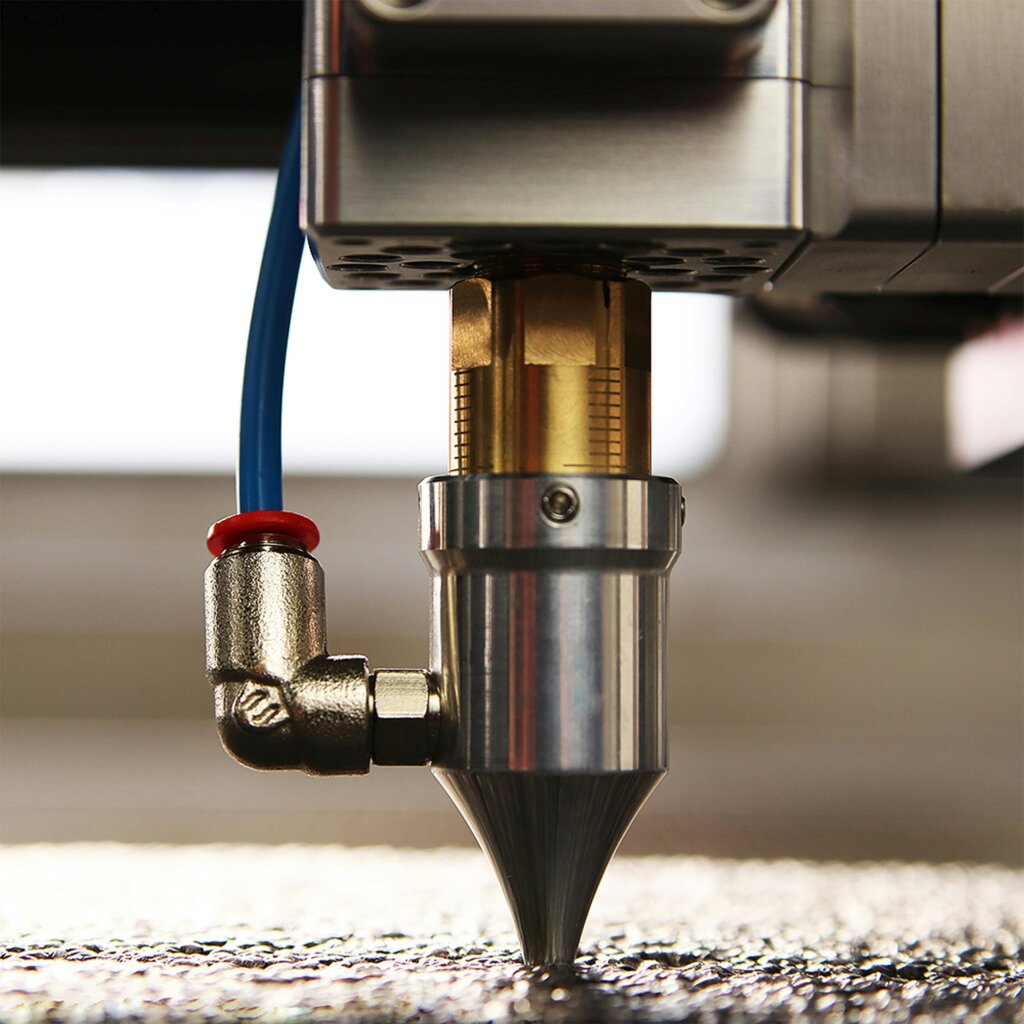
Axis Movement Problems (X, Y, Z):
Symptoms: Inaccurate movement, jerky motions, or failure to reach the desired position.
Causes: Problems with ball screws, linear guides, or the drive motors.
Solution: Lubricate or replace ball screws, check for any mechanical obstructions, and recalibrate the machine.
Drive Motor Failures
Symptoms: Lack of motion or unresponsive movement on one or more axes.
Causes: Faulty motor, damaged wiring, or issues with the controller.
Solution: Inspect and replace faulty motors or wiring, and recalibrate motor controllers
8 types of cnc machines Breakdown
Ball Screw and Linear Guide Wear:
Symptoms: Reduced precision, increased backlash, or misalignment.
Causes: Prolonged use, insufficient lubrication, or foreign debris.
Solution: Replace worn ball screws or guides, and clean and lubricate regularly.
2–Electrical Failures cnc machines Breakdown
Electrical components are critical for CNC operation, and failures in this area can lead to complete machine shutdowns.
Power Supply Issues:Symptoms: Machine not turning on, fluctuating or inconsistent power.
Causes: Faulty power supply unit (PSU), power surges, or improper grounding.
Solution: Inspect and replace the power supply, check fuses, and verify proper grounding
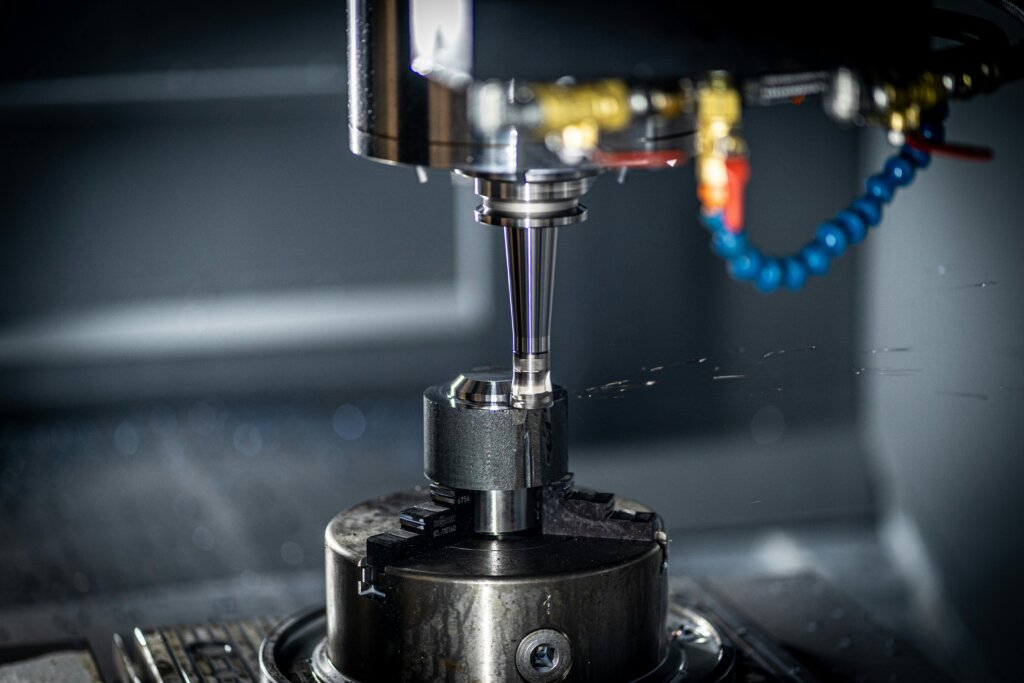
CNC Controller or Software Failure:
Symptoms: The machine may freeze, show error codes, or stop responding.
Causes: Corrupted software, faulty controller components, or improper calibration.
Solution: Reboot or reset the controller, reinstall or update software, and check for hardware malfunctions
Sensor or Encoder Failure:
Symptoms: Inaccurate positioning, unexpected stops, or unregistered movements.
Causes: Damaged sensors or encoders, electrical interference, or wiring issues.
Solution: Replace damaged sensors, clean the encoder, or replace faulty wiring.
3-Coolant and Fluid System Failures also cause of cnc machines Breakdown
The coolant system is essential for preventing overheating and improving tool life, so breakdowns in this system can severely impact machine performance.
Coolant Pump Failure:
Symptoms: Lack of coolant flow, overheating of the tool or workpiece.
Causes: Pump motor failure, clogging, or leaking hoses.
Solution: Replace or repair the coolant pump, clean hoses, and check for leaks.
Coolant Contamination:
Symptoms: Poor cutting performance, tool wear, or excessive heat.
Causes: Contamination of coolant, microbial growth, or degraded fluid.
Solution: Clean the coolant tank, replace contaminated fluid, and implement proper filtration.
4-Tooling Failures cnc machines Breakdown
Tooling issues can lead to poor part quality, reduced efficiency, or damage to the CNC machine.
Tool Breakage:
Symptoms: Chipped, broken, or worn-out cutting tools.
Causes: Incorrect tool choice, excessive load, improper cutting speeds, or material issues.
Solution: Replace the damaged tool, adjust cutting parameters, and ensure proper tool selection.
Tool Holder Malfunction
Symptoms: Loose tools, vibration, or improper tool fitting.
Causes: Worn-out tool holders or incorrect installation.
Solution: Inspect and replace tool holders, ensure tools are securely clamped.
5. Hydraulic or Pneumatic Failures (for specific machines) cnc machines Breakdown
Many CNC machines use hydraulic or pneumatic systems for tool changing, clamping, or movement, and failures in these systems can cause serious disruptions.
Hydraulic Pressure Loss:
Symptoms: Loss of clamping force, difficulty in tool changes, or erratic movement.
Causes: Low fluid levels, leaks, or damaged valves or pumps.
Solution: Inspect for leaks, replace damaged components, and ensure proper fluid levels.
Pneumatic System Failure:
Symptoms: Inconsistent or lack of pressure affecting the clamping system or tool changer.
Causes: Leaks, blocked valves, or compressor failure.
Solution: Inspect and replace faulty valves, check for leaks, or repair the compressor.
6. Mechanical Misalignment cause of cnc machines Breakdown
Symptoms: The machine’s parts fail to align correctly, leading to inaccurate machining or poor part finishes.
Causes: Wear and tear, improper installation, or mishandling.
Solution: Re-align the machine’s axes, recalibrate the CNC controller, and ensure proper installation.
7. Overheating Issues cause of cnc machines Breakdown
CNC machines operate at high speeds, and overheating can cause damage to sensitive components like the spindle or the controller.
- Symptoms: Machine stops unexpectedly, spindle motor warning, or excessive heat in certain areas.
- Causes: Insufficient coolant, high feed rates, or malfunctioning cooling systems.
- Solution: Ensure coolant is functioning properly, reduce the workload or speed, and inspect components for damage due to heat.
Communication Problems
CNC machines rely on smooth communication between the operator interface and the controller, and issues in communication can disrupt operations.
Symptoms: The machine fails to respond to inputs, or error codes appear on the display.
Causes: Loose cables, software bugs, or communication breakdowns between the controller and interface.
Solution: Check the wiring, reset or update the software, and reconfigure communication settings.
Preventive Maintenance Tips for Resolve cnc machines Breakdown
Regular lubrication and cleaning of components.
Scheduled inspection of mechanical parts, especially bearings and ball screws.
Calibration and software updates to prevent software-related breakdowns.
Timely replacement of worn-out parts like tools, belts, and seals.
Monitoring coolant levels and cleaning filtration systems.
By identifying and addressing the root cause of CNC machine breakdowns promptly, downtime can be minimized, and machine performance can be optimized.
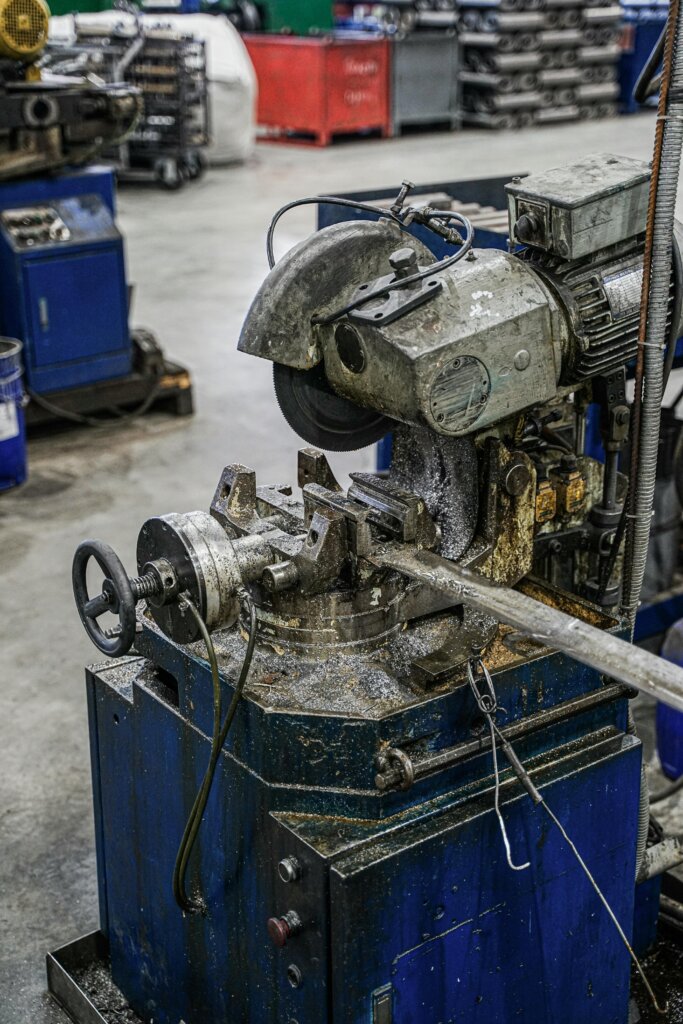
Read Also